Invited Speaker-----Dr. K.K. Ramachnadran
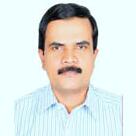
Department of Mechanical Engineering, Government Engineering College Thrissur, Thrissur – 680009, Kerala, India
Speech Title: Role of Intermetallic formation at the Joint Interface on Strength and Corrosion Characteristics of Dissimilar Friction Stir Welded Aluminium Alloy/Steel Joints
Abstract: Dissimilar joining of aluminium alloys and steels attracts significant research attention in the recent times due to their application criticality in automotive/ marine sectors in view of the fast depleting fossil fuel reserves and environmental degradation. Studies showed that in automotive/marine multi-material design concept for weight reduction, aluminium alloys can replace about 40 – 50 % of steel. But, the main obstacle is the difficulty in thermal joining of these materials due to their very low mutual solubility (promote intermetallic reaction) and huge difference in thermo-mechanical properties. Studies reported in the literature established that friction stir welding (FSW) is a viable technique for efficient joining of aluminium alloys and steels. Though intermetallic reaction is reported to be a critical hurdle in fusion welding, in dissimilar FSW of aluminium alloys and steels, it is confirmed that the formation of a thin iron-aluminium intermetallic (IMC) layer at the joint interface is conducive for better joint integrity. When dissimilar aluminium/steel joints are exposed to a corroding medium, galvanic corrosion occurs wherein the more active aluminium corrodes. To the best of knowledge, studies on dissimilar FS welded aluminium/steels joints that correlate the strength and corrosion behaviour with the IMC layer formation at the joint interface is missing in the literature. Therefore, in the present research, aluminium alloy AA5052 and HSLA steel are FS welded by varying the primary FSW parameters and the joint strength and corrosion behaviour are characterized. The joint interface microstructure is analysed using FESEM with EDS and EBSD and the corrosion behaviour is investigated using the electrochemical Tafel extrapolation technique. The studies showed that average IMC layer thickness of about 1 μm is essential for better joint integrity. The research further revealed that the electrical conductivity of iron-aluminium IMC’s is about 10% and 2% of the conductivity of iron and aluminium, respectively and in the galvanic series, the position of iron-aluminium IMC’s is in between that of iron and aluminium. Therefore, when a layer of IMC exists at the interface, galvanic couples will be formed between iron and IMC layer and IMC layer and aluminium. But, when the IMC formation is partial at the joint interface, the aluminium will be in direct electric contact with the steel and galvanic couple will be formed between them which results increased galvanic corrosion. The very detailed corrosion studies and analysis revealed that a thin layer of IMC throughout the joint interface is essential for good joint strength and better corrosion resistance.