Invited speaker---Dr. Jie Yin
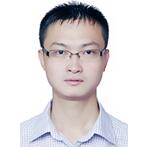
Dr. Jie Yin, Associate Professor of advanced carbide ceramics group, Shanghai Institute of Ceramics, Chinese Academy of Sciences (SICCAS)
Biography: Jie Yin (PhD, born in Aug. 1986), Asscociate Professor of advanced carbide ceramics group, Shanghai Institute of Ceramics, Chinese Academy of Sciences (SICCAS). After earning PhD degree in 2013, he conducted post-doc researches in KIMS and Alfred Univ. USA. He conducted systematic studies ranging from high-efficiency fabrication of advanced carbide ceramic to SiC-based composite materials during his oversea experience. He holds several research projects, such as Youth Innovation Promotion Association of CAS, Fund Program for the Scientific Activities of Selected Returned Oversea Researchers, NSFC and Science Foundation for Youth Scholar of State Key Lab in SICCAS, et al after returning back to SICCAS. He published more than 30 SCI papers in Scripta Mater., J. Euro. Ceram. Soc., J. Am. Ceram. Soc. during recent 5 years (20 as first/corresponding authors).
Title: Pressureless Densification, Microstructure Tailoring and Performance Optimization of Ta
0.8Hf
0.2C Solid Solution Ultra-high Temperature Ceramics
Abstract: Ta
0.8Hf
0.2C ceramics are candidate material for thermal protection systems as sharp leading edges, nose caps and flight control components of aerospace vehicles that can be exposed to extreme environments with temperatures exceeding 2000 °C by dissociated air operating at hypersonic speeds.
In our research, Ta
0.8Hf
0.2C-based ceramics were densified by pressureless sintering at 2200
oC for the first time up to a relative density of 98.83%. Relationship between the solid solution formation and pressureless densification was investigated. Solid solution formation decreased the activation energy for diffusion at grain boundaries and contributed to the final densification. Grain boundary pinning was used to tailor the microstructure of Ta
0.8Hf
0.2C by adding fine SiC particles (0.5 μm) successfully. The average grain size of matrix phase was decreased from 13.6 to 2.0 μm by the addition of 30 vol% SiC. The physical pinning assisted densification by optimizing the diffusion rate of grain boundaries to match with closed pores migration but inhibited the diffusion of Ta atoms into lattices of HfC at the pinned grain boundaries. The thermal properties and indentation toughness had been improved after the introduction of SiC while the flexural strength, elastic modulus and Vickers hardness decreased with SiC addition. The grain boundary pinning weakened the solution strengthening. However, the pinning side-effect provides us a new route to tailor the micro/nanostructure of solid solution by decelerating or even freezing the diffusion rate at the grain boundary.
Furthermore, Ta
0.8Hf
0.2C-27vol%SiC (99.0% in relative density) was toughened and strengthened via pressurelessly in-situ reactive sintering process. HfC and β-SiC particles were formed after reaction of HfSi
2 and carbon black at 1650°C. Ta
0.8Hf
0.2C was obtained from solid solutioning of HfC and commercial TaC. The β→α phase transformation of SiC proceeded below 2200°C. High aspect ratio, platelet-like α-SiC grains formed and interconnected as interlocking structures. Toughness and flexural strength values of 5.4±1.2 MPam
1/2 and 443±22 MPa were measured respectively. The toughening mechanisms by highly directional growth of discontinuous α-SiC grains were crack branching, bridging and deflection behaviors.
Keywords: Ta
0.8Hf
0.2C-SiC ceramic composite, Microstructure tailoring, Pressureless densification, Strengthen and Toughen, thermos-physical properties